U-FAST materials

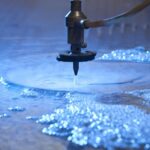
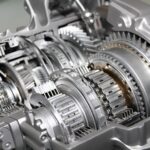
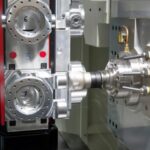
PPC materials
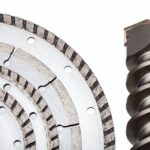
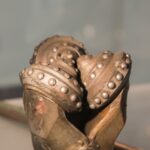
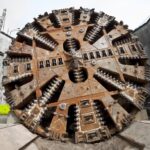
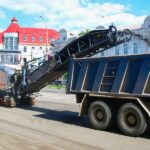
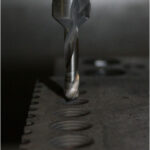

Sintered brakes and clutches
GeniCore researchs proved there is a big potential in U-FAST technology for materials used in automotive industry. Materials created with U-FAST technology can be used for brake discs and clutches which significanlty increases the possibility of the parameters designing for that applications. For brake discs the 40% weight reduction can be expected and improvement of NVH. Moreover, the particulate emission can be reduced up to 95%.

Waterjet nozzle
Nanocrystalline solid materials, due to their special structure, are often characterized by different properties, both physical (specific heat, thermal expansion, Curie temperature, etc.) and mechanical (strength, hardness, resistance to wear and erosion, etc.) as compared to conventional materials. One of the technologies for producing these materials is powder metallurgy, in which to achieve densification of the powders, the following techniques are used: free sintering, hot pressing, or hot iso-static pressing.
In the conventional powder technology, for the sintering of powders, sintering with simultaneous pressing is usually used. Sintering the powder in these processes occurs by diffusive transportation of the mass between the particles of the concentrated powder in the areas of contact, usually in the presence of a regulator, or of other substances, which assist in the destruction process of the oxide barriers hindering the diffusion. Due to the necessity of prolonged exposure to heat, these processes generally result in grain growth and loss of unique characteristics resulting from a nanocrystalline structure.
GeniCore solutions allow the preparation of nanocrystalline materials of high hardness and an increased resistance to abrasion. This goal is achieved both through the proper selection of the composition of the material (the possibility of using materials with, or without, a binding phase) and the use of GeniCore’s methods of sintering, which allow for a significant reduction of the unfavorable grain growth, thereby stopping the loss of unique properties, resulting from the nanocrystalline structure.

Automotive
The materials used for the blades of cutting tools should have a number of features to ensure their high durability. The most important of these are:
- high strength
- hardness and resistance to dynamic loads and fracture-cracking
- high chemical resistance
Materials that partly meet the above requirements are sintered carbides, produced by powder metallurgy methods. The characteristic microstructure of these materials, consisting of hard elements of carbides of tungsten, titanium, and the ductile binder cobalt phase, allows for the combination of opposite characteristics in a single material, high abrasion resistance, and hardness with high strength and good fracture-cracking toughness. The abrasive wear resistance of these materials can be significantly enhanced by replacing the part of the carbide aspect. The introduction of a high-hardness element (several times harder) to this type of composite will increase, significantly, the abrasion wear resistance, and the cobalt binder phase ensures adequate toughness of the composite.

Iron & Steel
Forming processes and processes offering final shape by machining losses, pose higher and higher requirements for the materials used for cutting tools. Ensuring the right quality of the surface and efficiency of the cutting process are the main challenges for materials and tools in the machining operation, with the simultaneous increase of requirements of the treated materials.
One of the directions in the development of tool materials, next to the CVD coatings, is the CUBNEC composite (Cubic Boron Nitride Enhanced Cemented Carbide). This material provides a high degree of hardness, guaranteeing resistance to abrasion, and the appropriate impact resistance which prevents the blade from chipping. GeniCore’s innovative, composite material can be successfully used in the process of turning, milling, and the grinding of materials in various industries, including iron-based materials.

Construction & Stone
In the tool market, there are many different types of drills called “diamond drills”. However, unlike the carbide-tipped drill (with a tip made of sintered carbide), complex cutting edges do not appear, only the diamond segments located at the edge of the tube. The diamond segments are metallic-sintered, in which the metallic matrix consists of low melting metal alloys, usually bronze. In these sinters, the combination of diamond particles with the matrix is usually mechanical in nature.
As part of its research work, GeniCore compiled a comparative analysis of the materials available on the market, destined for, among others, the edges of drills for making holes in natural stones like granite and marble, and in ceramic plates of gres types, with increased resistance to abrasion.
GeniCore solutions indicate that it is possible to significantly increase the durability of drills – by one hundred percent, whilst reducing the time needed for making the holes. GeniCore’s solution does not require the use of an impact in the drilling process, as the DEC-type diamond tools (diamond enhanced cemented carbide) do not require refrigeration as opposed to competing solutions.

Oil & Gas
The development of technologies for oil and gas exploration in recent years has been very dynamic, mainly due to the extraction of shale. The use of suitable drilling heads, in terms of their design and the material of the blade, is a key part of the extraction technology.
Drilling requires the use of extremely resistant materials that can cope with unpredictable operating conditions. Using the method of GeniCore sintering, a composite diamond-based material is obtained. This material used on ‘drill bits’ ensures long life through enhanced resistance to abrasion and impact. Thanks to the possibility of influencing the diamond particle size and the number of phases of the binding matrix in the composite material, GeniCore can meet various requirements flexibly, depending on drilling conditions.

Mining & Tunneling
The working conditions of modern materials assume extreme loads. This creates the need for new materials with higher strength parameters or modification of the properties of the traditional materials.
GeniCore solutions in the field of Mining & Tunnelling are tested on Faculty of Mechanical Engineering Tallinn University of Technology within the NeTTUN project (New Technologies for the Tunnelling Industry). NeTTUN receives funding from the European Commission’s Seventh Framework Programme for Research, Technological Development and Demonstration under Grant Agreement 280712.

Road maintenance
Thanks to the proper selection of the proportion and particle size, DEC, by GeniCore, the highest hardness and resistance to abrasion in the milling cutters’ ends is duly provided.
Proper selection of carbide grain size and the binding phase gives the DEC material the required toughness necessary within the process of milling the surface. The combination of these two parameters allows the DEC to reach a level of durability, unattainable for the sintered carbides used so far.

CFRP composite (Carbon - Fibre – Reinforced - Polymer)
Composite materials machining (fibre-reinforced) involves the increased use of composite materials, more and more. This is especially noticeable in the aviation, automotive, and consumer electronics industries. This poses special requirements for the machining methods. Particular emphasis is placed on
the strength of the tools and the quality of the machined surface, where the main problem is the delamination of the composite.
The tool material that can be used in many machining applications (drills, milling cutters, roto files) is based on a composite carbide diamond – DEC (diamond-enhanced cemented carbide). Its impact resistance, combined with a high degree of hardness, guarantees good-quality performance. The opportunity of applying the appropriate geometry ensures the quality of the surface after machining.