U-FAST COMPACT for R&D Applications
* Pressing force – possible options of hydraulic system or servopress.
** Max Current – The final value of the current is related to the value of the on-site connection voltage , so it can vary accordingly. Max output current can be increased up to 5 000 A.
The GeniCore U-FAST COMPACT model is a great choice for R&D applications where the aim is to develop new materials which can be then scaled up to bigger diameters by using GeniCore U-FAST GC (SPS) Device.
A vacuum chamber is a double-walled stainless steel construction supported by a steel frame. It is cooled by water that flows between the walls. The internal walls are thoroughly polished and protected by stainless steel reflectors, which are installed on the side walls and doors.
The doors open with hinges from left to right to allow material to be loaded and unloaded, and to inspect and maintain the chamber. Closing is carried out by means of two manually operated clamps.
The chamber is equipped with a set of sealed flanges for connection:
• Pumping system
• Actuator
• Viewing ports (sight glass)
• Safety valve
• Vacuum gauge port
• Thermocouple port
• Two additional spare ports
In the U-FAST COMPACT device the temperature is measured by pyrometers. The reading are recorded by the logic controller which enables easy control of the process and its subsequent analysis.
The temperature is controllable by a programmer (with several possible ramps and steps). The temperature controller (PLC module) can be connected with additional two type K thermocouples which can work with various temperatures including temperatures below 1000°C. Nevertheless, the GeniCore solution with additional side pyrometers covers full temperature range from RT to 2500℃, so the thermocouples are mainly an additional feature for scientific benefits.
The U-FAST COMPACT vacuum system includes:
• Rotary pump,
• Measuring sensors,
• Vacuum valve,
• Air admittance valve,
• Safety valve,
• Turbomolecular pump.
Thanks to an appropriate measurement system, the whole is managed by the automation system controlling the pump and valves.
The inert gas system supplies the chamber with gases. It consists of:
• Pressure relief valve
• Inlet valve
• Pressure gauge set for pressure measurement
• Mass Flow Controller for gases
The gas system will allow to introduce inert gas: argon, helium, nitrogen into the sintering chamber by using PLC controlled digital thermal mass flow controller for gases. It will allow to specify the percentage of the inert gas volume in the sintering chamber by using the U-FAST COMPACT HMI
Manufacturing process
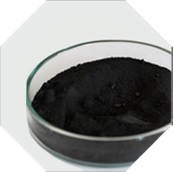
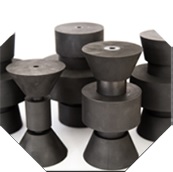
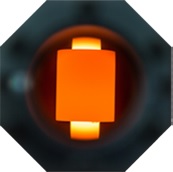
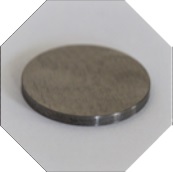
Mold inside U-FAST chamber

Temperature measurement

Conventional Method
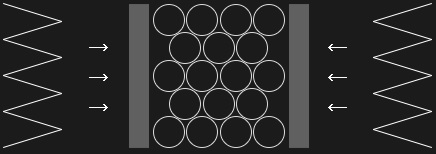
- Heating by radiation
- Low heating factor
- Temperature gradient in sintered materials
- Time-consuming and energy-consuming processes
U-FAST technology
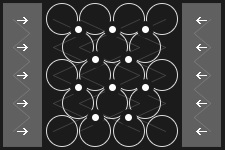
- Heating using Joule heating
- Fast, economical processes (30 min)
- Low energy consumption
- Lower sintering temperature
- Limited grain growth
Pulse duration below 1 ms
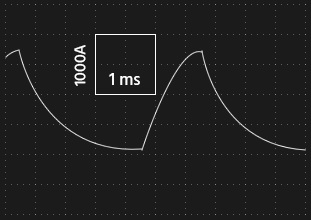
Pulse duration, which lasts even less than 1ms, gives the advantage of our U-FAST technology over SPS devices from competitors. Current pulses are shown using an oscilloscope
Download GeniCore Device Catalog
Send download link to: